Marble Factory Energy Solution
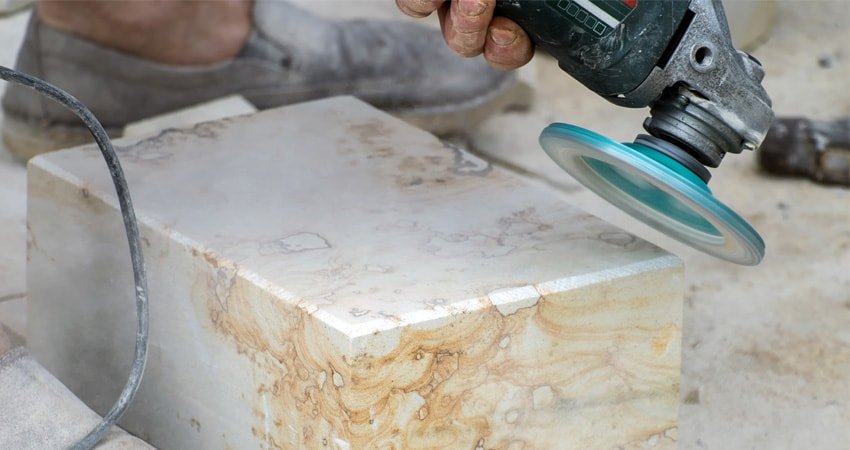
Problem
-
High energy consumption
Diagnosis
-
Measuring the energy consumption of marble cutting, cleaning and aligning machines in the factory and monitoring the measured values to uncover any undetected excess energy consumption
Solution
-
23 Energy Analyzer, Gateways and Monitoring Software were used. 1 Energy Analyzer was connected to the main transformer input in order to measure the total power and energy. A 100 meters long communication cable was installed from the distribution panel to the computer. The energy consumption in the factory was started to be monitored through the communication network by reading measurements from 22 Energy Analyzer that are connected to the machines and departments with high energy consumption.
-
It was revealed that the marble cutting machines draw 150 A currents instead of the nominal load current of 100 A, that the cutting blades went out of balance sooner than expected because of the excessive strain and that the cutting speed was 10 m² per hour instead of 12 m² like it should be. These issues were eliminated by making the necessary adjustments to the cutting machines.
-
A marble cutting machine (ESTE) has a nominal power of 110 kVA. It consumes about 80 kW of power in one hour. It means that an ESTE consumes 80 kW of power while cutting 12,5m² of marble in one hour. This amounts to €9 worth of electrical energy consumption per hour. Thanks to the installed monitoring system, energy consumption cost has been added to the product cost calculations and the selling prices were revised. A shift loss of 5 minutes for one worker amounted to a work loss of 26 hours in a year. This factory has the capacity to process 2 containers full of product in 26 hours and this production loss amounted to €20.600. The workers started to follow the shift times more carefully since they knew that the machines were being observed through the monitoring system, thereby eliminating labor loss.
-
When overtime was necessary, an overtime engineer had to be present even though only 3 workers were working. Thanks to the installed monitoring system, the working hours of machines and their energy consumption values were able to be monitored remotely, thereby eliminating the necessity of an overtime engineer and saving a minimum of €900 per month.
Conclusion
-
Thanks to all these measures taken, the electricity bill of the factory was decreased and the energy started to be used much efficiently. The installed system paid itself in 6 months by increasing the machine efficiencies and by decreasing the cost of the saw balance.