Textile Factory Energy Solution
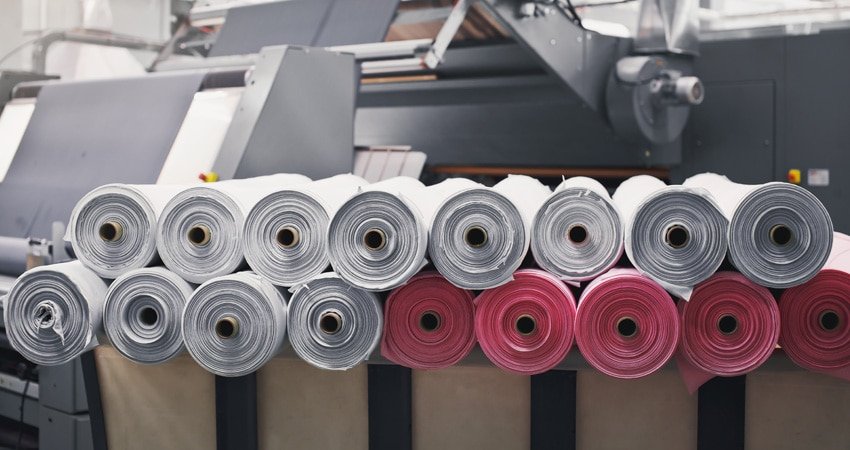
Problem
The textile factory is not able to monitor the energy meter that is attached to the main MV line. The factory would also like to monitor the consumption of loads that are connected to the 5 transformers that are connected to the main line.
Diagnosis
The factory needs a system that can measure the energy values periodically. The system should also be able to connect to generator outputs, to the loads that are connected to the transformers and to the reactive power control panel.
Solution
Integrate ENTES system with Energy Analysers, Energy & Power Meters and Power Factor Controllers. The system is available with software and is able to monitor from one central terminal. Total system for this company:
-
6 pcs Energy Analyzer
-
53 pcs Energy and Power Meter
-
3 pcs Power Factor Controller
-
2 pcs Gateways
-
1 wireless Ethernet Receiver-Transmitter
-
Monitoring Software
Description
With the new ENTES system the utility company’s energy meter at the main line could be monitored. The Energy Analyzer was also connected to this main line and the energy consumption of the line was double-checked by comparing the utility energy meter values to the ENTES analyzer energy values.
Secondly, the energy consumption of every section in the factory could be monitored. The consumption of the 3 different shifts were compared and the shifts with the most and least energy consumption were determined. After determining the energy consumption of every section, improvement operations were executed in order to decrease the energy consumption and work more efficient. Examples of the operations: bringing in motors with higher efficiency, taking precautions to provide better ventilating and cooling.
Another advantage of the system is that the costs of the generators for the facility could be calculated. Final important change to mention is that the company did not have to pay penalties anymore for the reactive energy. The values measured by the power factor controller were monitored from a remote computer thanks to the computer communication.
Conclusion
The possibility to avoid reactive energy penalties already brought a 13% decrease of the energy costs to the company. Thanks to the new energy management system, the sections and devices that consume excessive energy were recognized and the devices were replaced by devices that need less energy. Additionally, the sequence of the shifts was adjusted to avoid too much energy on the peak demand times of the facility. With the project cost at €12.000 the payback period was 3 months.